Trouble shooting ventilation challenges in sow barns
Sow farm ventilation ensures the environment in the barn is correct to maximize both piglet and sow comfort. First, we must understand what the optimum environment is for both a sow and her piglets and try to balance that to the best of our ability. When the sow is comfortable, she’s more likely to provide better for her piglets, thus weaning a stronger litter.
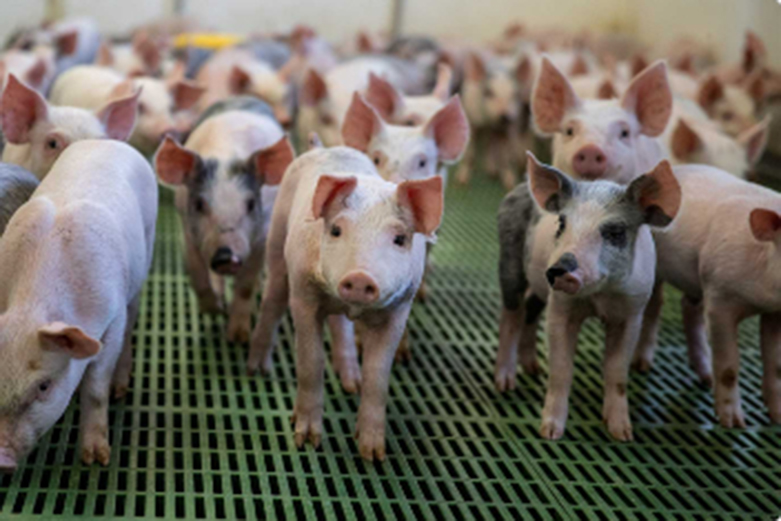
Achieving Desired Room Temperature (DRT)
Proper comfort starts with understanding the desired room temperature (DRT) during each production stage. The second step is setting and programming the proper curve to achieve the DRT at each stage. Determine the proper maximum and minimum ventilation strategy based on room design and season and adjust the temperature curve according to season and pig comfort.
Once programmed, check airspeeds (600-800 feet per minute from inlets) and humidity (<65%) with an anemometer such as the Kestrel 3000. A temperature curve is not one size fits all and will need adjustments based on its ability to achieve DRT, your farm, health status, seasonality.
Monitoring swine barn ventilation
Daily observations will help ensure the ventilation in your farm is running properly. Check and record high and low temperatures. Use tools such as an infrared thermometer to check comfort zone temperatures and a Kestrel to monitor air speed and humidity throughout the room and in the farrowing stalls. If an issue is identified or readings are outside of normal/expected operation, address it immediately rather than at the end of the day.
Watch pig behavior, it can tell you a lot about their comfort. Piling within a pen or stall indicates they are too cold. If they are spread out, they might be comfortable or hot. Pigs are social. They like to lay together, sometimes even with their head on their neighbor. These behavior cues can indicate an opportunity to improve comfort. Keep an eye out and adjust temperature curves, ventilation rates and inlets accordingly.
Troubleshooting common ventilation challenges
Think you’ve got a ventilation issue? Use these three steps to uncover and fix the culprit.
- Assess the room. Use sight, smell, a temperature probe, and Kestrel to understand what’s happening in that room.
- Check controller settings and adjust.
- Reassess the room. What’s changed? What hasn’t. Use sight, smell, a temperature probe, and Kestrel again.
The farrowing door is slamming shut
This usually occurs when the inlet or curtain opening does not match the extraction rate (or fan speeds) creating a vacuum effect. For example, wall inlets remaining closed to increase the wind speed of fresh air entering the room.
- Check if air speed at the inlet is meeting the goal. If not, check that the inlet or curtain opening is correct for the ventilation stage and the room temperature reading. Are all the fan belts and blades clean and running properly?
- Check the actual room temperature, temperature curve, current set point, fan stages, and bandwidth. Ensure all are correct given your SOPs for the given situation and stage of production.
- Wait 30 minutes and reassess. Is the door still slamming? Are the pigs comfortable? Check the next day in the heat of the day.
Sow respiratory rates are too high
A normal sow respiratory rate is 15-25 breaths per minute. A respiratory rate of more than 50 breaths per minute could threaten her and her litter. This often occurs in the summer if temperatures rise above 78°F within the room and outdoor temperatures are above 90°F with a heat index above 100°F.
- Check inlet or curtain openings; they should all be open to achieve an air speed of 600 FPM during maximum ventilation. Next, check fans to ensure stages are running properly and that the fans are clean. Check that cool cell pads are wet evenly and that the airspeed through the cool cell is 300-400 FPM. Check that all drippers are working properly, if applicable.
- Check that the current set point and bandwidths are set correctly based on the production stage; the room temperature is likely over the set point. Fan stages should be set to 100% capacity during maximum ventilation to achieve maximum cooler capacity. Set bandwidth to 1°F during late ventilation stages. Ensure cool cells and drippers are set to turn on at 12-16°F above set point. Manually check thermostat and probe readings to make sure they are accurate.
- Inside the room, make sure all ceiling inlets fed by cool cells are open. If they are not fed by a cool cell, they should be closed to minimize the amount of hot air entering the room from the attic. If your farm is filtered, ensure the filters are not plugged. Turn all heat lamps off and check flow rate at the water nipple (1/2 gallon per minute). Lastly, ensure cool cells are getting enough water and it is evenly distributed across the pads.
Cool cells are not cooling
On warmer days, cool cells that do not get water may increase sow respiratory rates due to improper cooling or incorrect airspeed. When cool cells are functioning correctly, they can help cool a room by 8-20°F. Remember to check humidity level within the room when using cool cells, the goal is to remain below 65%.
- At the cool cell system, check that air speed is 300-400 feet per minute through the pad. Check that the water supply is turned on and the tank has water in it. Ensure the pump is functioning properly and is not stuck or clogged.
- At the controller, see if the set point is at the point where a cool cell should be running. If cool cells do not run through the controller, check that the thermostat that controls temperature is set correctly for the pump to turn on.
- Inside the room, make sure all wall inlets or curtains are open and ceiling inlets are open if they are drawing cool cell air through the ceiling. Ensure all heat lamps are off.
Remember! Even the smallest tear in a curtain, a gap under a door, or a broken inlet can cause a draft or pocket of hot or cold air (dependent on season). For more information on sow farm ventilation, check out these podcasts: Sow Farm Ventilation Part 1 and Sow Farm Ventilation Part 2.